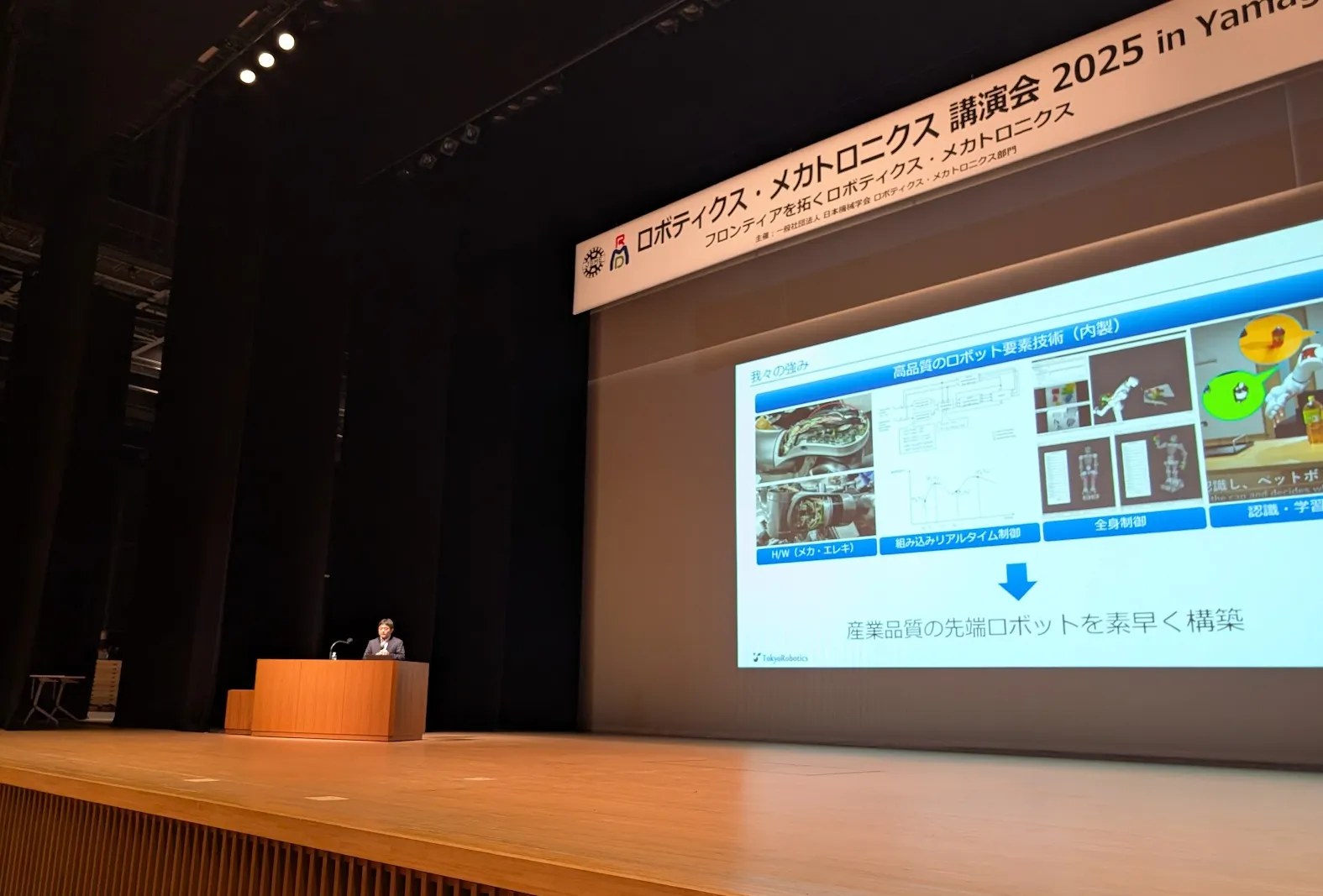
2025-06-04
Our CEO, Sakamoto, gave a talk at Robomech 2025 held in Yamagata City.
We aim to create a world where robots do repetitive and hazardous tasks, while humans engage in work that requires their mind and heart.
We apply the latest robotic technology to create new solutions that satisfy undiscovered needs. We ultimately aim to create general-purpose robots that can perform a variety of tasks and to introduce them into various markets.
Torobo is a humanoid robot designed for use in a variety of fields, including manufacturing, logistics, and service. By using high-performance torque sensing and impedance control throughout its body, Torobo can perform tasks safely and skillfully.
Our CEO, Sakamoto, gave a talk at Robomech 2025 held in Yamagata City.
Our CEO, Sakamoto, gave a pitch at the SAKURA DEEPTECH SHIBUYA Moonshot Collaboration Project.
Our CEO, Sakamoto, gave a talk at a pharmaceutical company's in-house seminar.
Yoshihiro has been involved in the robotics and positioning (indoor and outdoor navigation) fields for over 15 years. He has worked as a researcher in Waseda University and as a freelance engineer. He has acquired a wide range of skills and knowledge throughout his career: robotics, satellite navigation, machine learning, embedded system, RF circuit design, FPGA coding, Windows application development, web system development, and server management. He received his Ph.D. from Waseda University in 2013 on the theme of indoor positioning with GPS-compatible signals. He is now interested in constructing a business based on robotics technologies. He likes studying history.
After completing his Ph.D., he worked at RIKEN and Waseda University, where he was engaged in research on cognitive robotics, which uses neural networks and robots to model and understand human cognitive abilities. He then worked on the development of automatic driving technology using AI at Denso Corporation, and on the research and development of reinforcement learning for business applications at ALBERT Inc. His hobbies are sports.